OEM Quality from series Supplier: Relying on quality also for spare parts – with seals from Corteco
Corteco does not compromise when it comes to spare parts. The independent aftermarket unit of Freudenberg Sealing Technologies is closer to series development than most other suppliers. You can see the key differences between OEM quality and cheap products at the latest when you visit the test field in Weinheim. This makes the products interesting not only for end customers, but also for the independent aftermarket.
A warranty with a clear conscience, thanks to OEM standards
Freudenberg Sealing Technologies, which Corteco belongs to, is a technology expert and global market leader for sophisticated and innovative applications in sealing technology – and this makes it an important partner for customers in a wide range of industrial sectors. From automotive and robotic production to heavy-duty applications, such as construction and agricultural machinery, the product range covers almost every type of use. The company also sells its high-quality products to the independent aftermarket under its own Corteco brand. For the Weinheim-based company, it goes without saying that the same standards apply here as for series production.
“Applying the quality of series production directly to the independent aftermarket is not an additional expenditure for us, it’s a logical consequence. We benefit from our wide-ranging experience and the very strict requirements of series development in the automotive sector,” says Dr. Christian Dickopf, Senior Vice President Corteco.
Automotive is and remains in the premier class
Pharmaceuticals, robotics and automotive – these are the industries that Robert Leins thinks of first when he is asked about particularly stringent requirements. The head of the test field at Freudenberg Sealing Technologies in Weinheim (Germany) has just made his area fit for the future, using an investment of 3 million euros for e-mobility. This is where the seals undergo rigorous tests to ensure that they will perform their tasks reliably down the road – over a service life of 300,000 km. The laboratory is the largest of its kind worldwide and can model every conceivable application under reproducible test conditions. This is often the crucial advantage when it comes to the placement of new series orders.
“The individual OEMs have different requirements – all of them are high,” says the engineer, “For us, it’s always a matter of transferring the reality into our laboratory and reproducing it in fast motion. After all, you can’t put every seal on the road for 300,000 km to find out whether it can stand up to the demands. Here it takes 240 hours to complete an average test cycle.”
Reality in fast motion
If there are any questions about which requirements Leins is referring to, it becomes clear with a closer look at the more than 300 test stations. There is a funnel with mud, for example, in which a shaft is turning. Protecting the oil on the other side from contamination is the task of the radial shaft seal from Freudenberg Sealing Technologies. The test ranges from visible impurities to a chemical analysis, which reliably detects even minimal quantities.
And it isn’t just mud, Leins explains. Each use case requires its own test setups and substances: Nothing is left to chance here, not even the dirt. There is DIN dust for the German market, China dust for the Asian market and Arizona dust for North America – where a certain concentration of salt also has to be added. Each manufacturer has its own specifications and priorities.
“Most cars are sold and driven globally,” says Leins. “So you not only have to comply with the legal requirements of numerous countries but also take all possible climatic conditions into account. The OEMs take the easy road, so to speak, and plan for the toughest and most stringent applications. This means that customers can drive the same car in the rainforest, the Sahara or the Arctic Circle.”
In some regions of China or Alaska, temperatures can reach as low as -40 °C; the seals must also be able to withstand heat of up to 140 °C for long periods. But Freudenberg Sealing Technologies also likes to push the boundaries now and then: During cold tests, the components are exposed to temperatures as low as -60°C to identify the limits of what is technically feasible.
In addition to the standardized dust and temperature, factors include pressure, acids, bases, oils, UV radiation and dynamic as well as mechanical stresses due to wave impact or friction. The seals must also withstand water pulses of up to 100 bar and pass a test for ice water surges, which can occur on a downhill drive in winter, for example. Because one thing is certain: Seals also play an important role from an environmental perspective. The seals are installed in ferries and tugboats on Lake Constance, for example, the largest fresh water reservoir in Germany. Having a leak here would be particularly bad. In the chemical industry, seals also have to reliably hold off substances that can be highly toxic.
But the test field work does not stop at the seals. Just to produce the right test shafts, Leins has developed his own methods in his laboratory. The shaft must correspond precisely to reality: If the surface is too smooth, no oil film will form; if it is too rough, the seal also wears out quickly. In other words, the expertise of Freudenberg Sealing Technologies goes far beyond just the seals.
“Every seal only ever works in conjunction with the tribological system: For example a shaft, the medium and the seal. Additional factors come into play for each individual component, such as the surface quality, material and chemical composition,” Leins explains.
Understanding the sealing system in its entirety – this is another competence that the automotive market leaders value in Freudenberg Sealing Technologies. As a result, the team is often asked about its views on trends and gets involved in series development very early on. One example of this is a completely new requirement as a result of the rising e-mobility: The inverters in the battery-powered vehicles generate frequency inputs in the bearing points, which have the effect of small lightning strikes. Freudenberg Sealing Technologies offers the solution with electrically conductive radial shaft seals, which dissipate the charge around the bearing via the housing.
Leins and his team are particularly intrigued by the extremes and limits of what is technically feasible: From shafts with a one-meter diameter for shipbuilding to electric motors with 36,000 revolutions per minute, everything that has to meet the highest requirements is tested in Weinheim.
End customer’s benefit
At Freudenberg Sealing Technologies and Corteco, no seal leaves the factory without first undergoing rigorous tests. This results in premium spare parts that are at least as good as the originals used by the manufacturer. And for the repair shops and distributors, this translates into satisfied customers and no complaints. Car owners are pleased with the noticeable quality that sustains their car’s performance.
“The fact is that compared to the price of a car, a seal that costs a few euros is not worth any risk. Why compromise when you can rely on proven series technology that has been thoroughly tested? At Corteco, you will get a reliable product with uncompromising series quality,” Dickopf concludes.
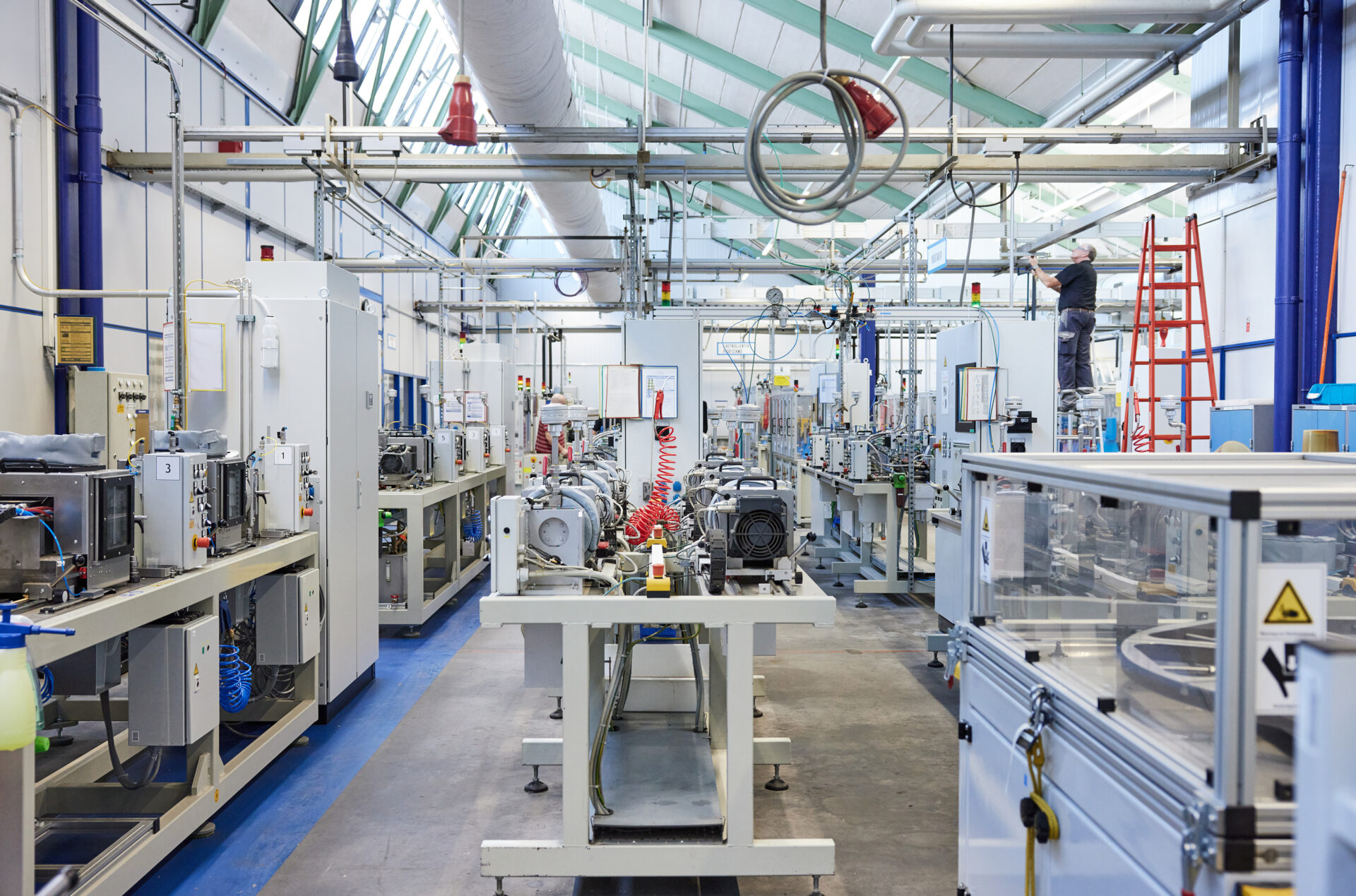
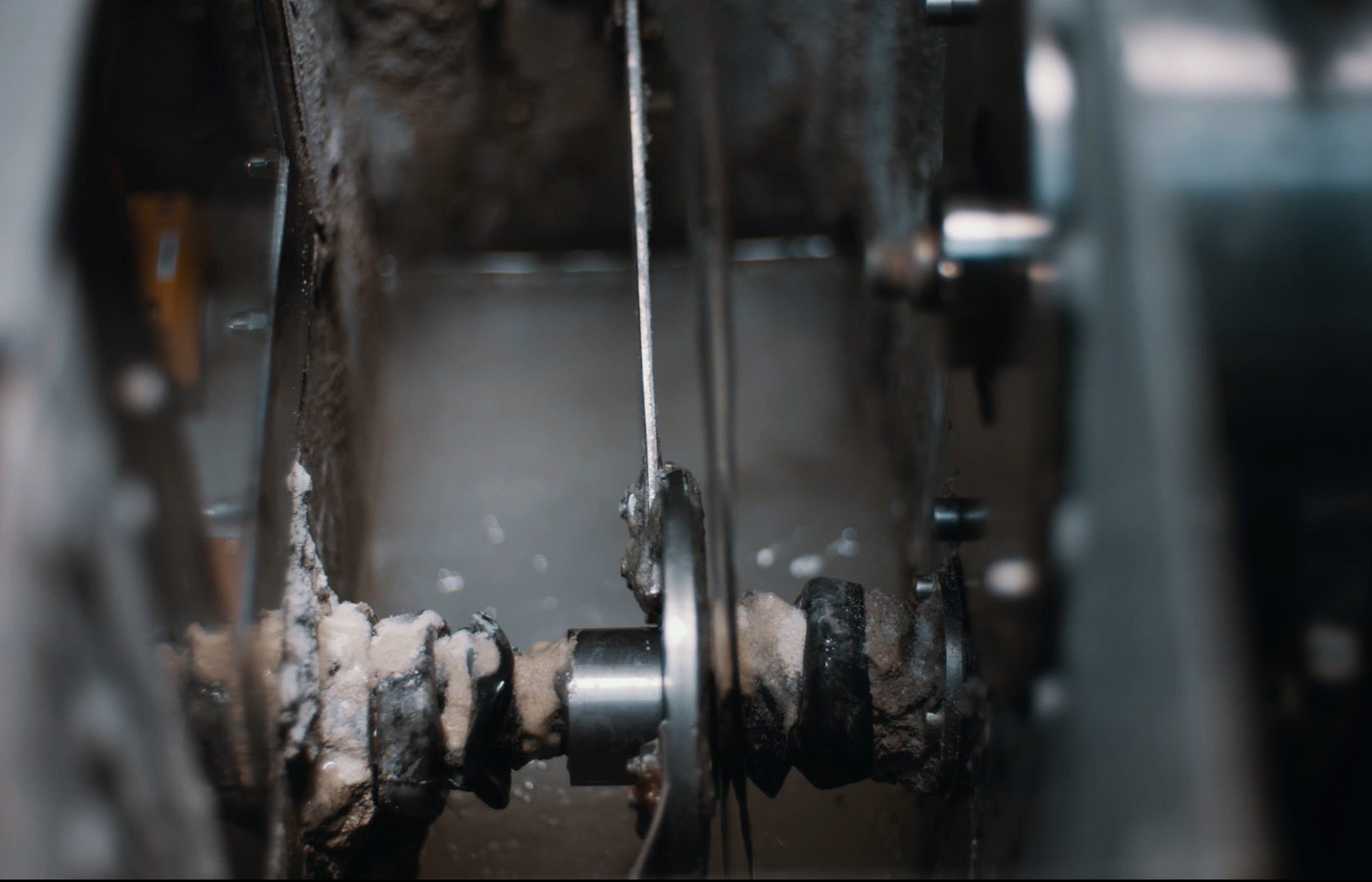
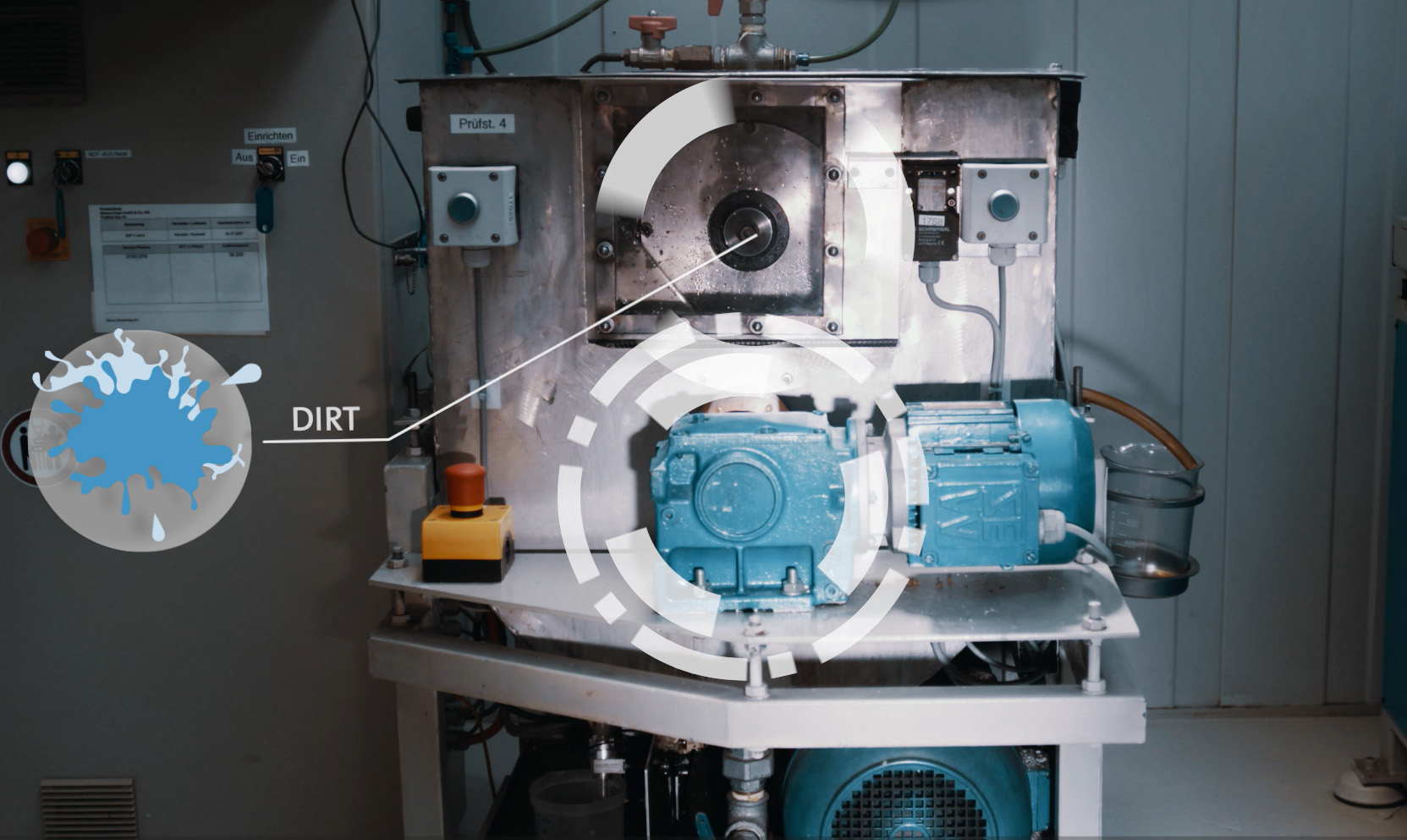
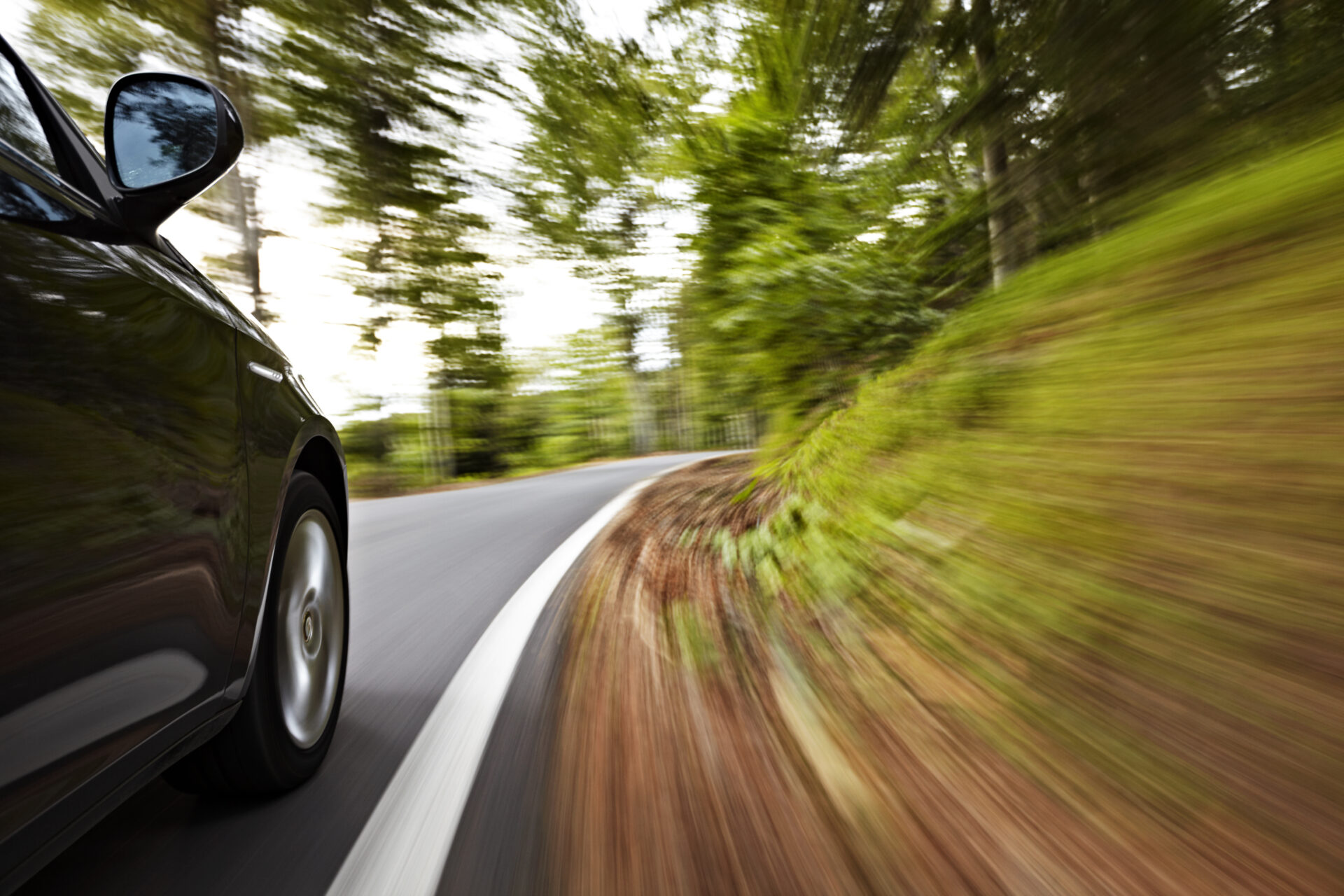
About Corteco
Corteco is one of the leading suppliers of components for the Independent Automotive Aftermarket. As a member of the global Freudenberg Group, we supply over 26,000 products in OEM quality. Independent garages trust in Corteco spare parts and therefore benefit from the original quality made by Freudenberg.
Freudenberg Sealing Technologies is a longstanding technology expert and market leader for sophisticated and novel applications in sealing technology and electric mobility solutions worldwide. With its unique materials and technology expertise, the company is a proven supplier for demanding products and applications, as well as a development and service partner to customers in the automotive industries and in general industries. In 2022, Freudenberg Sealing Technologies generated sales of about 2.45 billion euros and employed approximately 13,500 people. More information at www.fst.com
The company is part of the global Freudenberg Group which has four business areas: Seals and Vibration Control Technology, Nonwovens and Filtration, Household Products as well as Specialties and Others. In 2022 the Group generated sales of more than 11.7 billion euros and employed more than 51,000 associates in around 60 countries. More information is available at www.freudenberg.com