Invisible Player, Visible Impact: Reliable independent aftermarket solutions for the heavy-duty segment
At Corteco, the benefits of high-quality products are extremely well-known. No wonder – after all, the independent aftermarket unit of Freudenberg Sealing Technologies focuses on seals in more detail than nearly anyone else. Where one may not notice any difference at first glance, the devil, as so often, is in the detail. The example of radial shaft seals clearly shows how much development expertise is involved. This is particularly interesting for the independent aftermarket in the heavy-duty segment.
Aftermarket with OEM quality
Freudenberg Sealing Technologies, to which Corteco belongs, is a technology expert and global market leader for sophisticated and innovative applications in sealing technology – and this makes it an important partner for customers in a wide range of industrial sectors. From automotive and robotic production to heavy-duty applications, such as construction and agricultural machinery, the product range covers almost every type of use. The company also sells its high-quality products to the independent aftermarket under its own Corteco brand. The same standards apply here as for the company’s series production, which makes the products interesting for the demanding heavy-duty segment as well.
“Applying the quality standards of series production directly to the independent aftermarket is not an additional expenditure for us, it’s a logical consequence. We benefit from our wide-ranging experience and the very strict requirements of series development, especially in the automotive sector. These can also be applied perfectly to the heavy-duty market,” says Dr. Christian Dickopf, Senior Vice President Corteco.
Heavy-duty applications with special requirements
There are no all-encompassing solutions for the requirements in the heavy-duty segment: Each use case must be considered on its own. Corteco’s many years of experience in the automotive and truck sectors always come into play. The seals undergo rigorous tests to ensure that they will perform their tasks reliably down the road – over a service life of 300,000 km. The established standards also provide advantages in the heavy-duty segment.
Robert Leins heads the test field at Freudenberg Sealing Technologies in Weinheim, Germany, – which is also the largest of its kind in the world. Over 3 million euros were invested in its expansion in the last three years to ensure that new e-mobility demands would be met.
“The individual OEMs have different requirements – all of them are high, especially in the heavy-duty sector,” says the engineer. “For us, it’s always a matter of transferring the reality into our laboratory and reproducing it in fast motion. After all, you can’t put every seal on the road for 300,000 km to find out whether it can stand up to the demands. Here it takes 240 hours to complete an average test cycle.”
Reality in fast motion
If there are any questions about which requirements Leins is referring to, it becomes clear with a closer look at the more than 300 test stations. There is a funnel with mud, for example, in which a shaft is turning. Protecting the oil on the other side from contamination is one of the tasks which the seals from Freudenberg Sealing Technologies have to master. The test ranges from checking visible impurities to a chemical analysis, which reliably detects even minimal quantities.
And it isn’t just mud, Leins explains. Each use case requires its own test setups and substances: Nothing is left to chance here, not even the dirt. There is whole-grain flour dust for agriculture, DIN dust for the German market, China dust for the Asian market and Arizona dust for North America – where a certain concentration of salt also has to be added. A great deal must be considered particularly in the heavy-duty sector: In some areas, agricultural and construction machinery can easily be exposed to 1,000 times the load of a vehicle on a road.
Since no one can know exactly where a car or machine will ultimately be used, it must be tested to ensure all requirements are fulfilled. In some regions of China and Alaska, temperatures can reach as low as -40 °C; in addition, the seals must be able to withstand heat of up to 140 °C for long periods. But Freudenberg Sealing Technologies also likes to push the boundaries now and then: During cold tests, the components are sometimes exposed to -60°C for internal evaluations of which levels are technically feasible.
In addition to the standardized dust and temperature, factors include pressure, acids, bases, oils, UV radiation and dynamic as well as mechanical stresses due to shaft runout or friction. The seals must also withstand water pulses of up to 100 bar and even pass an ice water surge test on a downhill drive.
But the test field work does not stop at the seals. Freudenberg has developed its own methods in its laboratory just for producing the right test shafts. The shaft must correspond precisely to reality: If the surface is too smooth, there will be no oil film; if it is too rough, the seal wears out quickly. In other words, the expertise of Freudenberg Sealing Technologies goes far beyond just the seals.
“A seal only ever works in conjunction with the tribological system: For example the shaft, the medium and the seal itself. Additional factors come into play for each individual component, such as the surface quality, material and chemical composition,” Leins explains.
Understanding the sealing system in its entirety – that is another competence which customers value in Freudenberg Sealing Technologies. As a result, the team is often asked about its views about trends and gets involved in series development at a very early stage. One example of this is a completely new requirement as a result of the rising e-mobility. The inverters in the battery-powered vehicles generate frequency inputs in the bearing points, which have the effect of small lightning strikes. Freudenberg Sealing Technologies offers the solution with electrically conductive radial shaft seals, which dissipate the charge around the bearing via the housing.
Heavy duty as a beneficiary
Something that is already exposed to such massive loads on the road will also hold up in a field – or so you would think. But even here, special aspects must still be considered – such as the above-mentioned whole-grain flour dust.
“The fact is that a seal that costs just a few euros will protect an investment worth several hundred thousand. So why compromise when you can rely on proven series technology that has undergone rigorous tests? With Corteco, you will get rigorously tested products with uncompromising series quality,” Dickopf concludes.
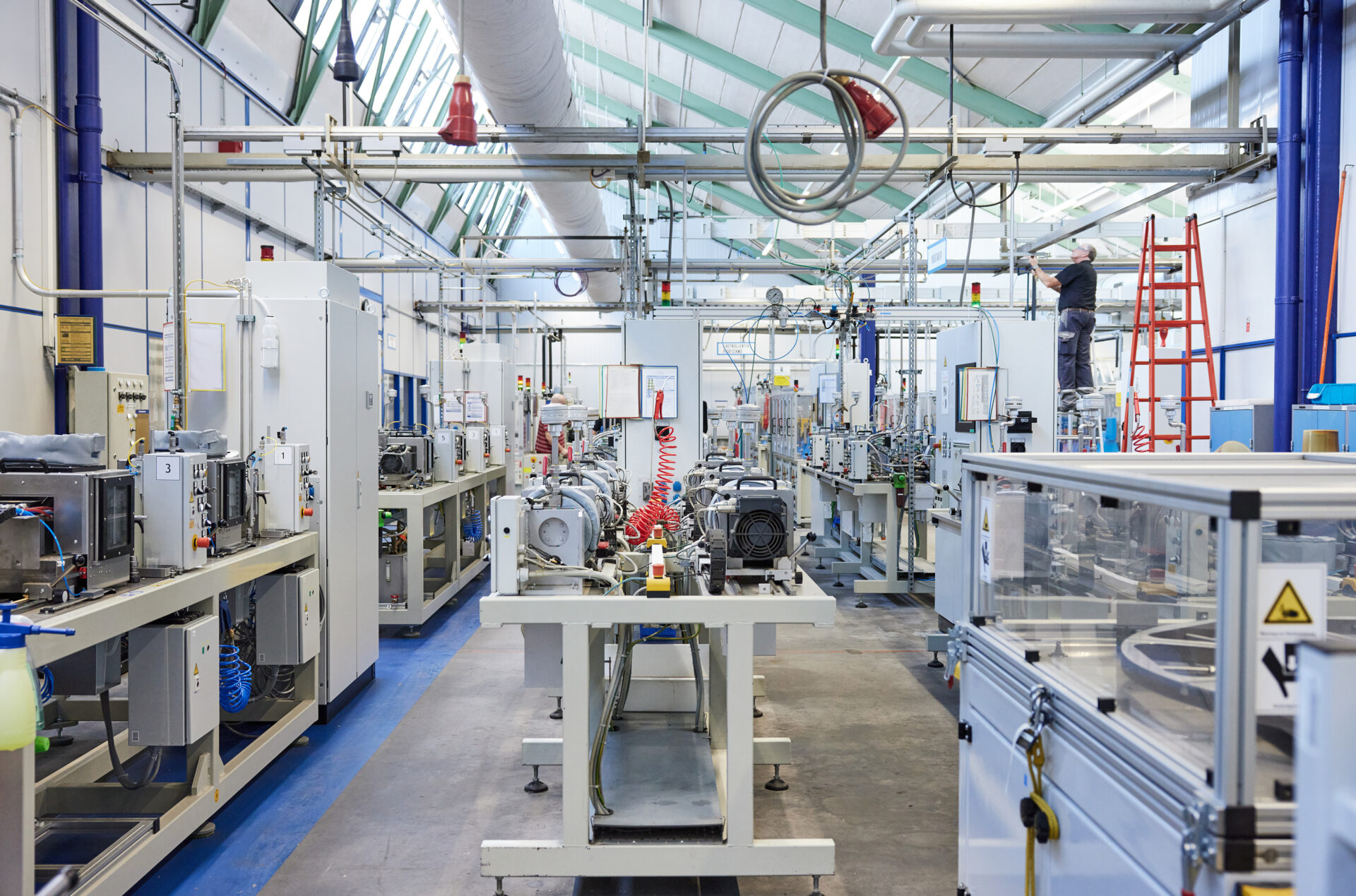
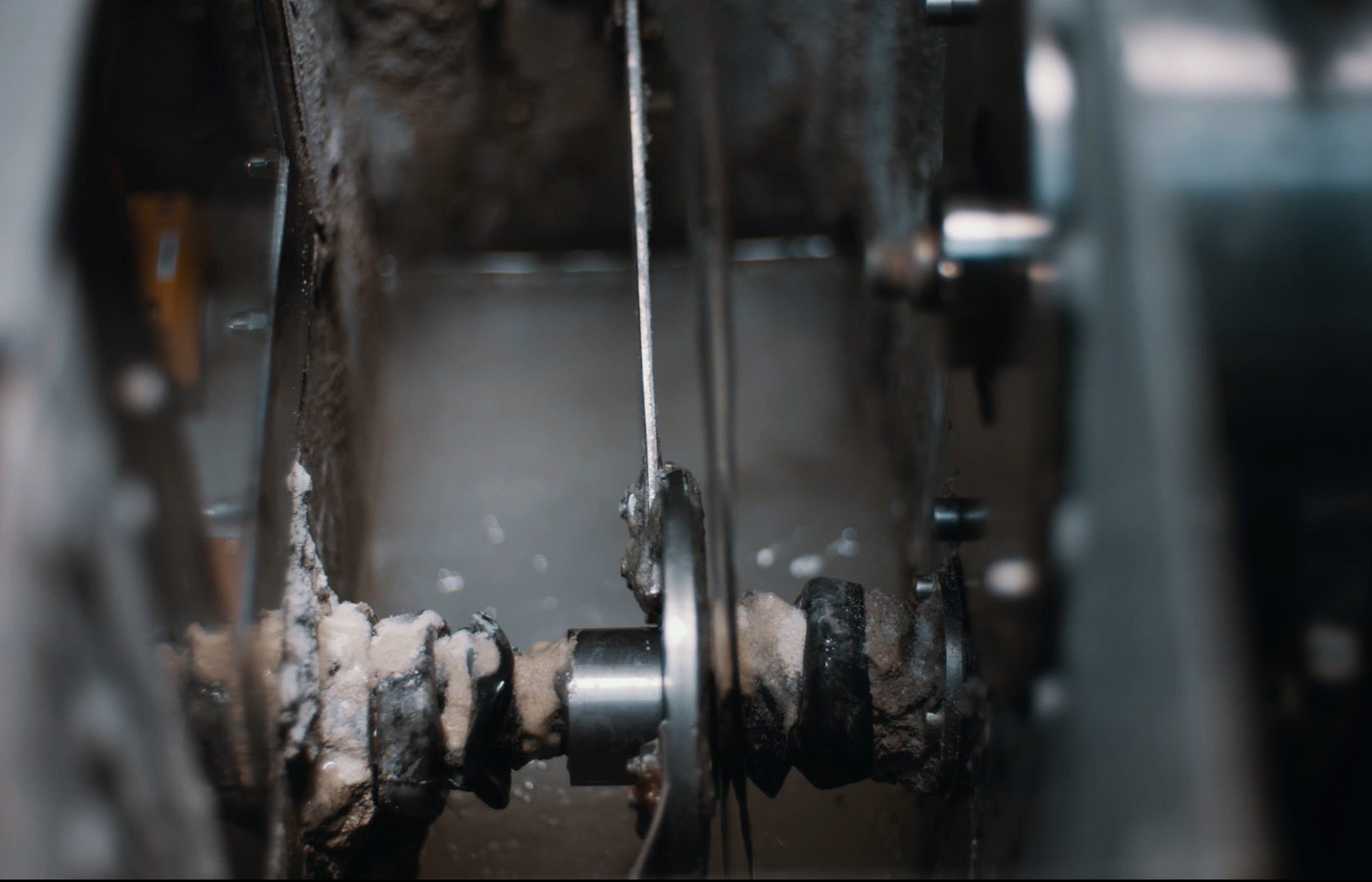
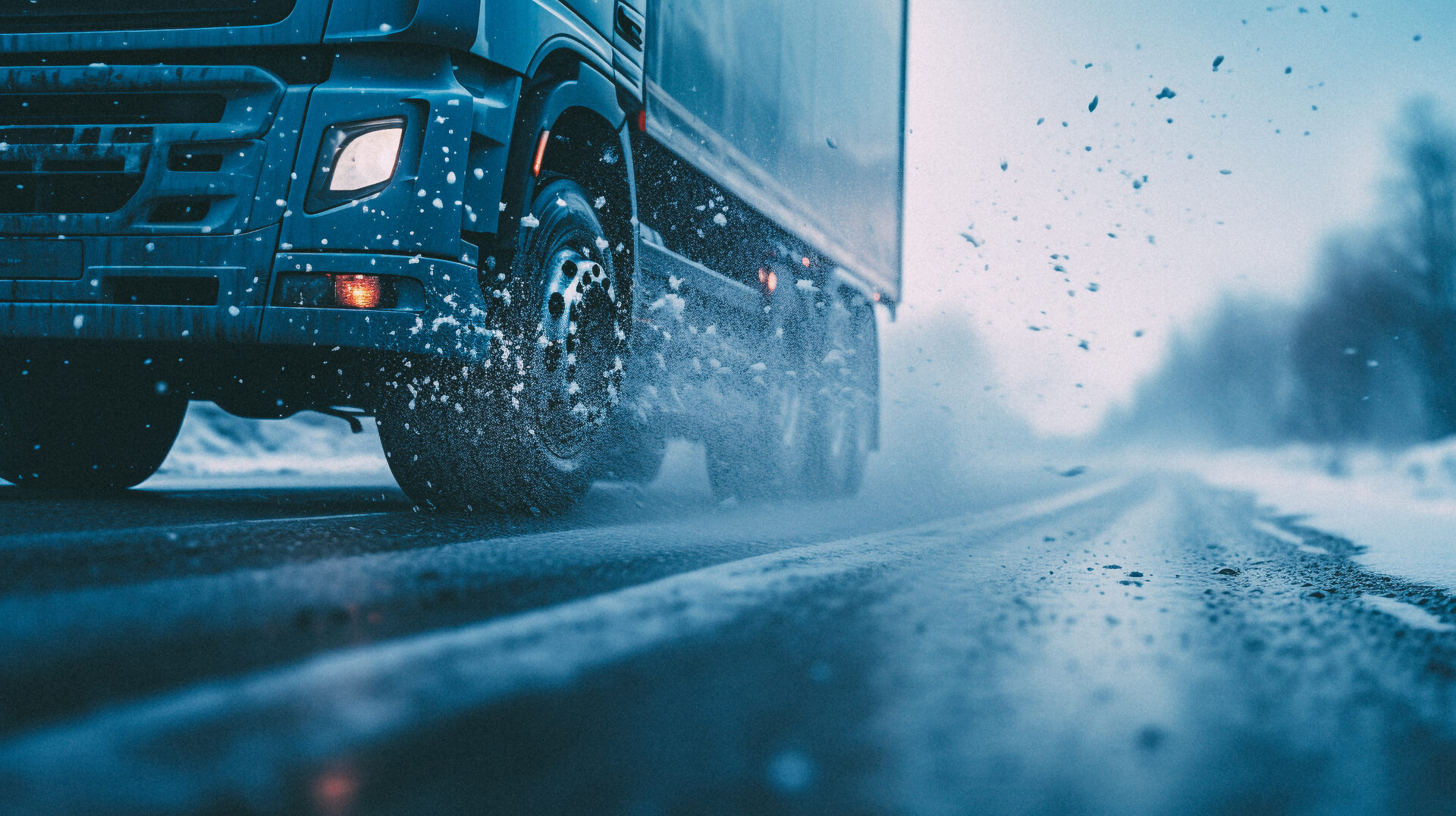
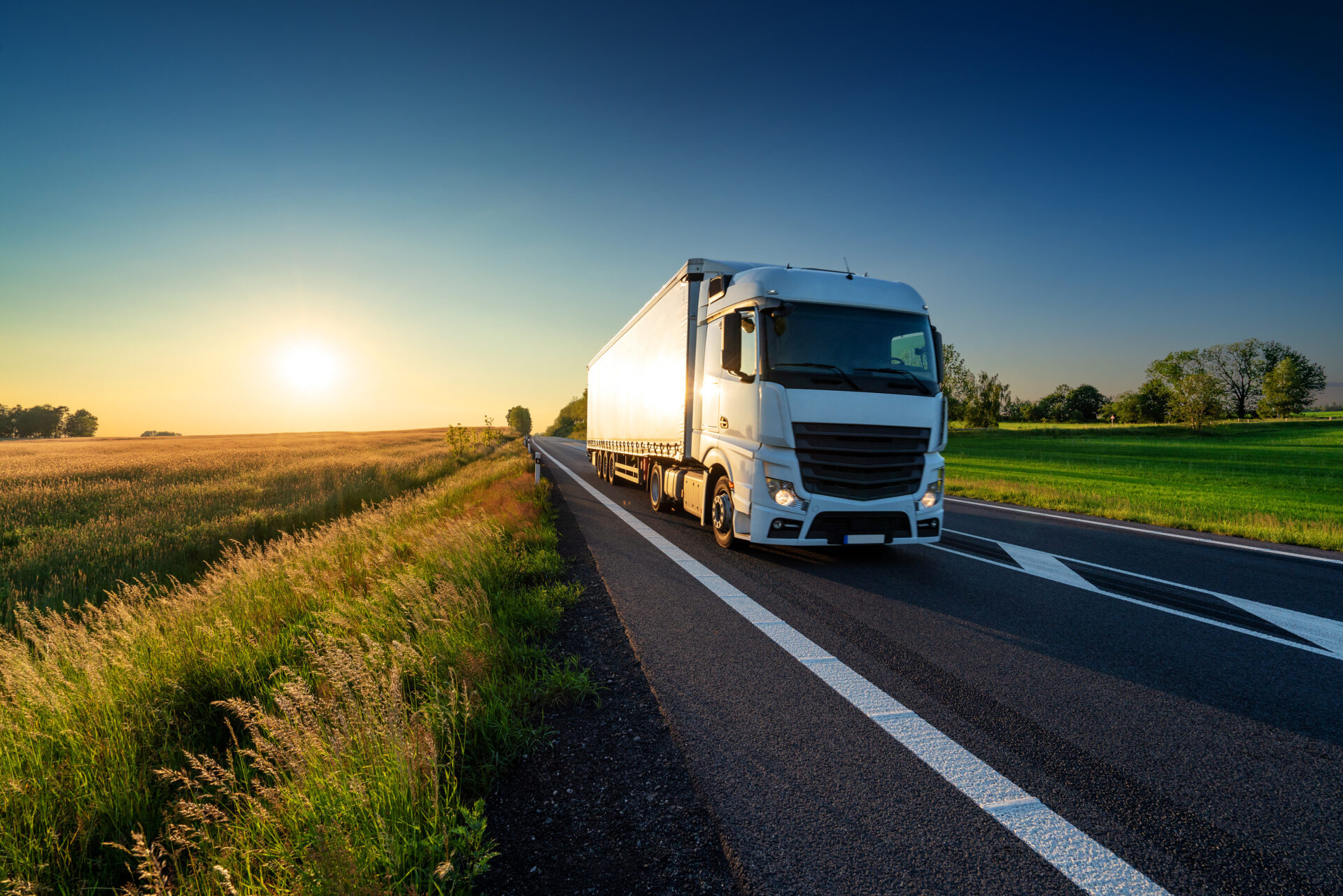