Unsichtbarer Beitrag, sichtbare Wirkung: Verlässliche Independent-Aftermarket-Lösungen für das Heavy-Duty-Segment
Bei Corteco kennt man die Vorteile von Qualitätsprodukten sehr genau. Kein Wunder, denn die Independenten-Aftermarket-Einheit von Freudenberg Sealing Technologies beschäftigt sich so detailliert mit Dichtungen wie kaum jemand sonst. Wo für den Laien auf den ersten Blick kein Unterschied zu erkennen ist, steckt der Teufel wie so häufig im Detail. Am Beispiel von Radial-Wellendichtringen wird deutlich, welch große Entwicklungsleistung darin steckt. Das ist gerade auch für den freien Ersatzteilmarkt im Heavy-Duty-Segment interessant.
Aftermarket in OEM-Qualität
Freudenberg Sealing Technologies, zu dem Corteco gehört, istTechnologieexperte und weltweiter Marktführer für anspruchsvolle und neuartige Anwendungen in der Dichtungstechnik – und damit wichtiger Partner für Kunden aus verschiedensten Industriezweigen. Von Automotive über Robotik bis hin zu Heavy-Duty-Anwendungen wie Bau- und Landmaschinen deckt die Produktpalette fast jeden Einsatzfall ab. Unter der Eigenmarke Corteco vertreibt das Unternehmen seine hochwertigen Produkte auch im Bereich des Independent Aftermarkets. Dass dabei dieselben Standards gelten wie für die Serienproduktion, macht die Produkte gerade auch für das anspruchsvolle Heavy-Duty-Segment interessant.
“Die Serienqualität direkt in den freien Ersatzteilmarkt zu übernehmen, ist für uns kein zusätzlicher Aufwand, sondern eine logische Konsequenz. Dabei profitieren wir von unseren weitreichenden Erfahrungen und den sehr strengen Anforderungen der Serienentwicklung, gerade aus dem Automotive-Bereich. Diese lassen sich ideal auch für den Heavy-Duty-Markt nutzen“, sagt Dr. Christian Dickopf, Senior Vice President Corteco.
Heavy-Duty-Anwendungen mit besonderen Ansprüchen
Bei den Anforderungen im Heavy-Duty-Segment gibt es keine pauschalen Lösungen: Jeder Anwendungsfall muss gesondert betrachtet werden. Dabei greift man bei Corteco auf die langjährige Erfahrung aus dem Automotive- und Truckbereich zurück. Hier werden Dichtungen auf Herz und Nieren getestet, damit sie später zuverlässig ihre Aufgabe erfüllen – und zwar über 300.000 km Lebensdauer. Die einmal gesetzten Standards sind auch im Heavy-Duty-Segment von Vorteil.
Robert Leins leitet das Testfeld bei Freudenberg Sealing Technologies in Weinheim – weltweit übrigens das größte seiner Art. In den vergangenen drei Jahren wurde es mit über 3 Millionen Euro Invest erweitert, um neue Anforderungen aus der E-Mobilität abbilden zu können.
“Die Anforderungen der einzelnen OEM sind unterschiedlich – hoch sind sie alle, gerade im Heavy-Duty-Sektor”, sagt der Ingenieur. “Bei uns geht es immer darum, die Realität in unser Labor zu übertragen und im Zeitraffer wiederzugeben. Man kann ja nicht jede Dichtung erst 300.000 km auf die Straße schicken, um herauszufinden, ob sie den Anforderungen standhält. Ein durchschnittlicher Testzyklus ist hier in 240 Stunden abgeschlossen.”
Realität im Zeitraffer
Welche Anforderungen Leins meint, versteht man spätestens, wenn man sich die über 300 Prüfstellen genauer anschaut. Da findet sich zum Beispiel ein Trichter mit Schlamm, in dem sich eine Welle dreht. Das Öl auf der anderen Seite vor Kontamination zu schützen, ist unter anderem die Aufgabe der Dichtungen von Freudenberg Sealing Technologies. Die Prüfung reicht von sichtbaren Verunreinigungen bis hin zur chemischen Analyse, die selbst Minimalmengen zuverlässig erkennt.
Auch dass es nicht einfach nur Schlamm sei, erklärt Leins. Jeder Anwendungsfall erfordert eigene Prüfaufbauten und -substanzen: Hier wird nichts dem Zufall überlassen, noch nicht mal die Verschmutzung. Da gibt es Vollkornmehlstaub für die Landwirtschaft, DIN-Staub für den deutschen Markt, China-Dust für den asiatischen und Arizona-Dust für Nordamerika – wo übrigens noch eine bestimmte Konzentration Salz beigemischt werden muss. Gerade im Heavy Duty Bereich gibt es da eine Menge zu beachten: So sind Land- und Baumaschinen in manchen Bereichen leicht der 1.000fachen Belastung eines Fahrzeugs auf der Straße ausgesetzt.
Da man am Ende nie weiß, wo ein Auto oder eine Maschine eingesetzt wird, müssen alle Anforderungen durchgetestet und erfüllt werden. In bestimmten Gegenden Chinas oder Alaska werden Temperaturen bis zu -40 °C erreicht, und auch Hitze bis zu 140 °C müssen die Dichtungen über längere Zeit standhalten. Bei Freudenberg Sealing Technologies geht man aber auch gern mal über die Grenzen hinaus: bei Kältetests werden die Bauteile auch mal
-60°C ausgesetzt, um intern die Grenzen des technisch Machbaren auszuloten.
Zusätzlich zu genormtem Staub und Temperatur kommen Druck, Säuren, Basen, Öle, UV-Strahlung und sowohl dynamische als auch mechanische Belastung durch Wellenschlag oder Reibung. Auch Wasserpulse von bis zu 100 bar oder eben den Eiswasser-Schwalltest von der Bergabfahrt müssen die Dichtungen bestehen.
Aber die Arbeit im Testfeld hört nicht bei den Dichtungen auf. Allein für die Herstellung der richtigen Test-Wellen hat Freudenberg in seinem Labor eigene Methoden entwickelt. Die Welle muss genau der Realität entsprechen: Ist die Oberfläche zu glatt, kann sich kein Ölfilm bilden; ist sie zu rau, verschleißt die Dichtung ebenfalls schnell. So geht die Expertise von Freudenberg Sealing Technologies weit über die reine Dichtung hinaus.
“Abdichtung funktioniert immer nur im Zusammenspiel des tribologischen Systems: Zum Beispiel der Welle, dem Medium und der Dichtung selbst. Bei jeder einzelnen Komponente kommen dann wieder weitere Faktoren hinzu, wie Oberflächengüte, Material und chemische Beschaffenheit“, erklärt Leins.
Das Dichtungssystem in Gänze verstehen – auch diese Fähigkeit schätzen Kunden an Freudenberg Sealing Technologies. So wird das Team häufig nach seinen Ansichten zu Trends befragt und in sehr frühem Stadium in die Serienentwicklung einbezogen. Ein Beispiel dafür ist eine komplett neue Anforderung, die durch die E-Mobilität entstanden ist. Die Umrichter in den batteriebetriebenen Fahrzeugen erzeugen Frequenzeinträge in die Lagerstellen, die wie kleine Blitzeinschläge wirken. Die Lösung liefert Freudenberg Sealing Technologies mit elektrisch leitfähigen Radial-Wellendichtringen, welche die Ladung um das Lager herum über das Gehäuse ableiten.
Heavy Duty als Profiteur
Was schon auf der Straße so massiven Belastungen ausgesetzt ist, das hält auch auf dem Acker – so könnte man denken. Tatsächlich sind aber auch hier noch Besonderheiten zu beachten – wie zum Beispiel der erwähnte Vollkornmehlstaub.
„Fakt ist: Eine Dichtung für wenige Euro schützt ein Investitionsobjekt im Wert von mehreren Hunderttausend. Warum also Kompromisse machen, wenn man auf bewährte Serientechnologie setzen kann, die auf Herz und Nieren geprüft wurde? Mit Corteco erhält man auf Herz und Nieren getestete Produkte in kompromissloser Serienqualität“, resümiert Dickopf.
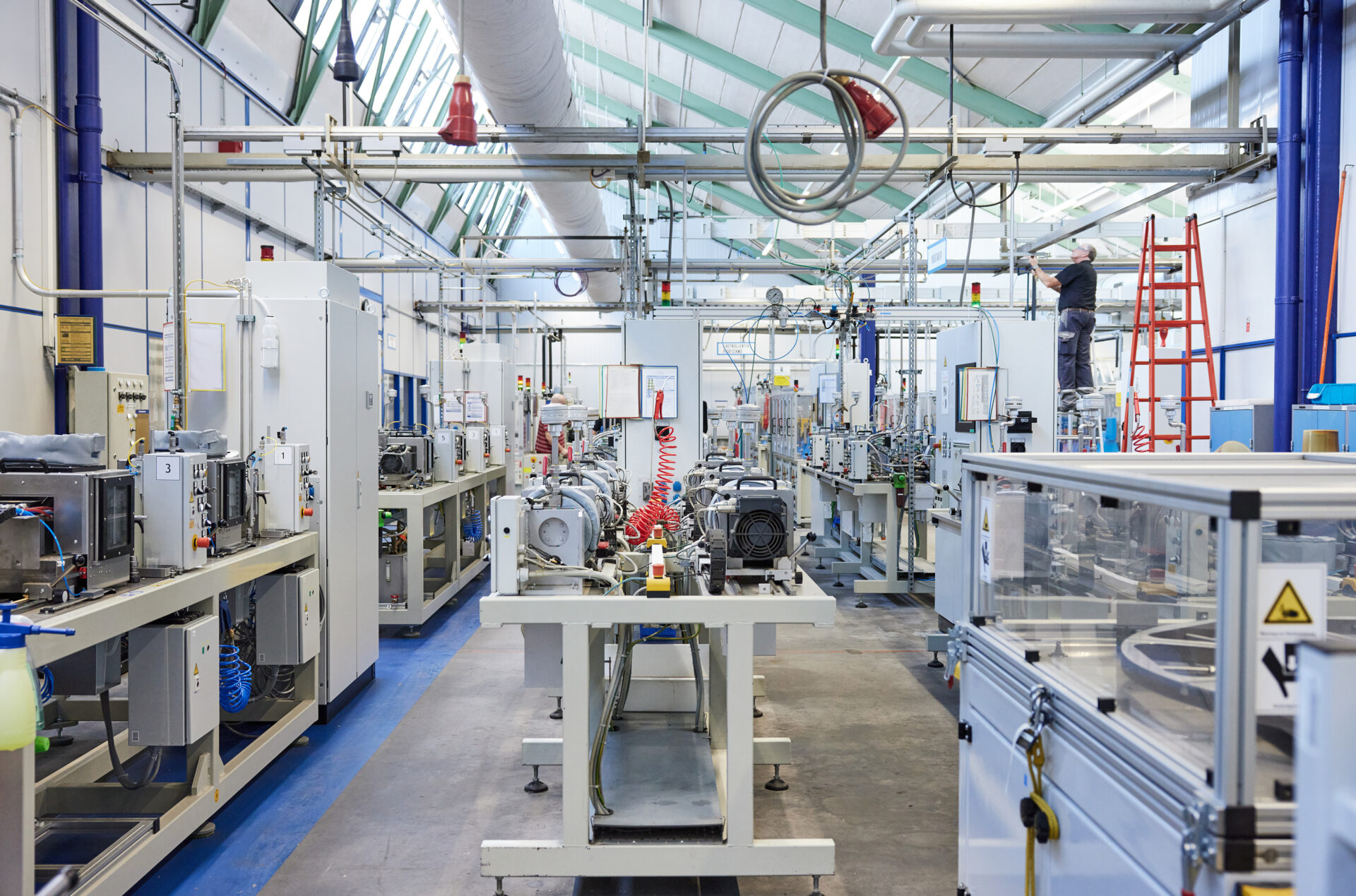
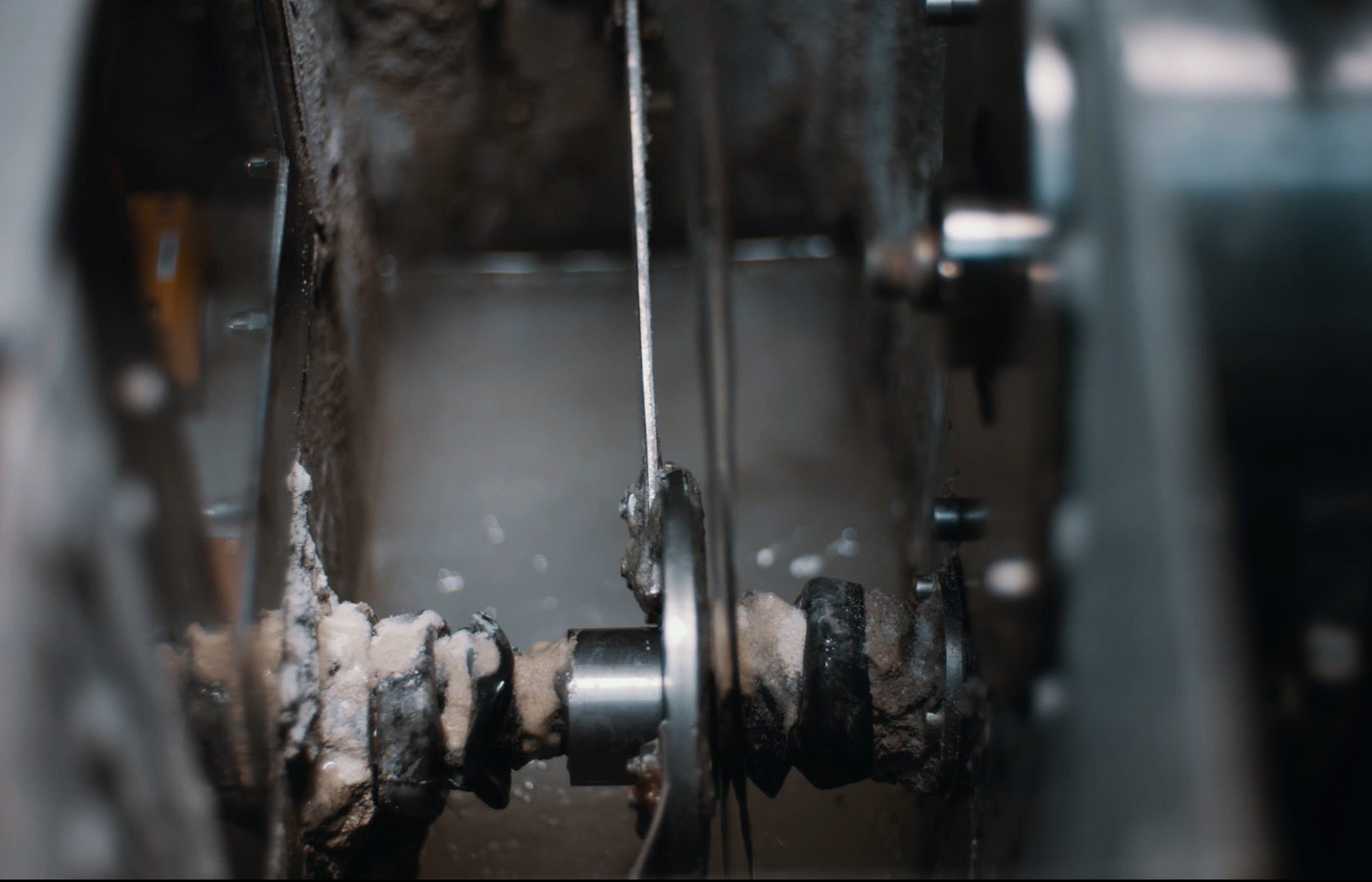
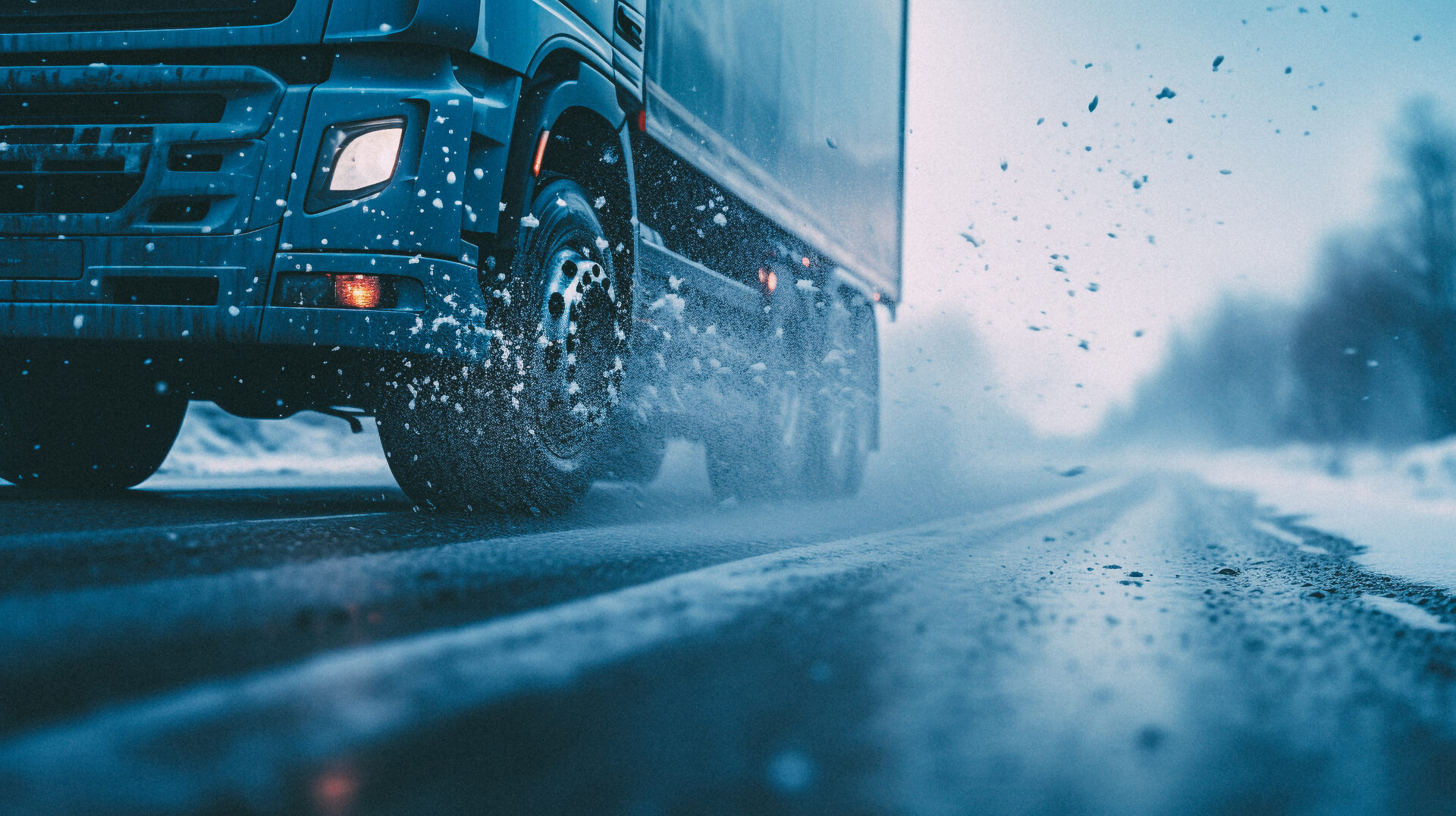
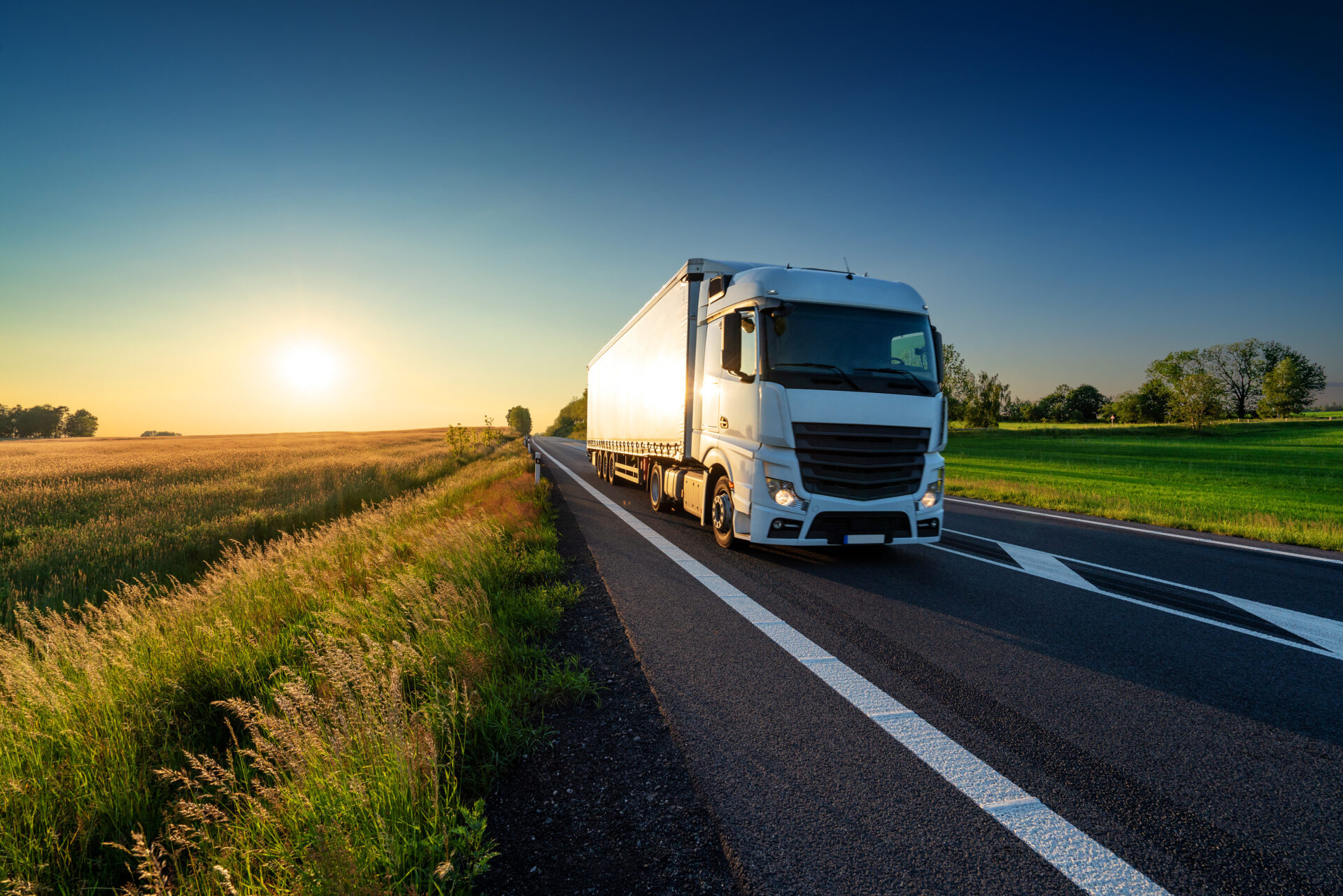