Corteco to Expand Capacity with New Warehouse
One of the leading international suppliers for the Independent Automotive Aftermarket invests in a new building and modern warehouse infrastructure.
Weinheim/Hirschberg. With its business growing and the e-transformation poised to increase demand for space, aftermarket auto parts supplier Corteco will begin building a new distribution center in Weinheim in 2024 to boost its warehouse capacity. It will be built in the Weinheim Industrial Park, near the Freudenberg Group headquarters.
The demand for warehouse space has exceeded the capacity of its current European logistics center in Hirschberg (Bergstrasse). Corteco, a top international supplier to the independent automotive aftermarket, is also gearing up for the e-transformation’s impact on its business in the medium term.
Corteco, a subsidiary of Freudenberg Sealing Technologies (FST), serves independent workshops whose customers naturally want their cars repaired quickly. That means spare parts have to be readily available. Corteco offers more than 26,000 articles in OEM quality, and about 16,000 of them, mainly sealing and vibration control parts and cabin air filters, are available from the Hirschberg facility. It ships about 100,000 parts to automotive service facilities each day.
The Hirschberg center has been in operation since 2013 and has a storage area of about 9,000 square meters (97,000 square feet). But with the growth in Corteco’s business, that will certainly not be enough in the future. Since the existing warehouse could not be expanded, plans were developed for a new building, and Corteco chose the Weinheim Industrial Park as the site for it, in part due to its existing infrastructure. The work is due to start in early 2024, and the move-in is planned for mid-2025.
“With 13,800 square meters (about 149,000 square feet), the new building will not only be larger – it will also provide us with an automated storage solution,” says Dr. Christian Dickopf, Corteco’s Senior Vice President. “We are planning on more growth in the future. Even if the impact of the e-mobility transition lags, we have to think about the products associated with it today.”
There will be an area in the new building where staff can assemble and package parts, making it possible to bring back operations that had been outsourced due to limited space and capacity. To put the matter in perspective: More than 95 percent of the parts distributed by Corteco are assembled into kits.
“Customers do not accept partial deliveries from different locations. They want everything in one package from one source. But relocating assembly operations to a potentially cheaper location would neutralize any cost advantages because of the extra transport costs. We would become slower and have longer lead times. This would put us at a competitive disadvantage, especially in the spare parts market. So that is not an option,” explains Dr. Wolfgang Lohmann, Director Operations in Europe.
There will be a high-bay warehouse and an Autostore system in the new building. Autostore is a space-saving, partially automated system that reduces the need for floor space by almost a third. Robots quickly perform physically demanding, repetitive tasks while optimizing the use of space. This lets employees focus on activities requiring their special expertise. “A full 99 percent of all the different articles we sell can be stored in Autostore. It can be expanded as required, even during ongoing operations, that is, without temporarily shutting down warehouse activities,” Project Manager Jan Mittelstädt explains.
Another benefit is that Autostore uses energy-efficient robots. When 10 of them are in operation, they consume no more energy than a vacuum cleaner. They “see” in the dark, don’t need wide aisles, and quickly find the items they are looking for. “The goods come to the people, not the people to the goods,” says Mittelstädt.
Sustainability is a key element of the project: A photovoltaic system will supply the facility with a significant share of its electricity. Packaging is also being improved, with “even less plastic” being the guiding principle.
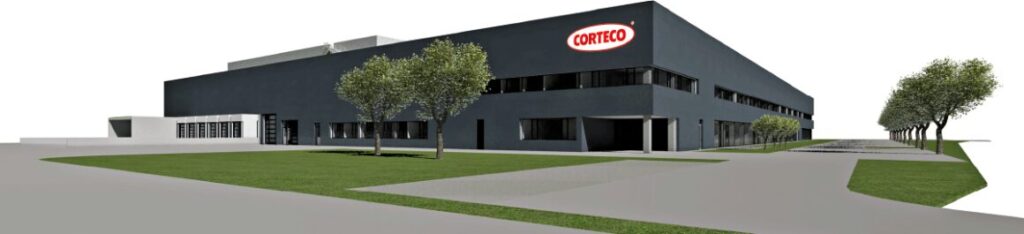